What is ACP?
Aluminium composite panels (ACP) are flat panels, typically 3mm – 5mm in thickness, consisting of two thin aluminium sheets bonded to a non-aluminium core, commonly made of polyethylene (PE), polyurethane (PU), or mineral fibre, or a combination of these components.
The PE core of ACP is the key driver of the recent product ban, due to its combustibility and potential to contribute to rapid fire spread on the exterior of the building.
The NSW Government (Dept. Fair Trading) has advised that fires which are associated with ACP with a polyethylene (PE) core pose a safety risk, especially when installed in multi-story buildings.
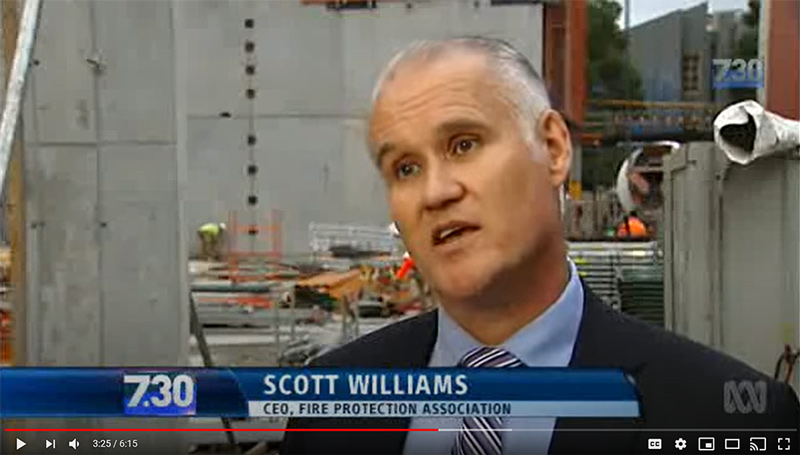
Why The Ban?
The NSW government’s ban follows the tragic Grenfell Tower fire in London in June 2017 which claimed 72 lives, the Lacrosse Building fire in Melbourne in November 2014, and similar fire events in China, France and the United Arab Emirates, the severity of which has been attributed to the installation of ACP cladding with a PE core.
Beware the 30% red-herring.
Three key concepts:
BCA/NCC
Compliance
The National Construction Code has long required the external walls of (most) buildings to be non-combustible.
Does my building comply with the non-combustibility requirements of the BCA/NCC?
Did it ever comply?
Is the ACP cladding the building’s ‘external wall’ or an ‘attachment’?
NSW
FAIR TRADING
BAN
NSW Fair Trading has used consumer protection/safety legislation to only ban the most unsafe/combustible type of ACP.
ACP with >30% PE core.
Yet, ACP with <30% PE is still combustible and incapable of passing the non-combustibility requirements of the NCC/BCA – AS1530.1.
Say what?
Life
Safety
Do I feel safe living or working in a building clad in ACP?
Do prospective purchasers want to buy a unit in a building clad in ACP?
Importantly, ‘compliance’ doesn’t necessarily = safety.
Life safety trumps ‘compliance’.
Council can now order you to remove the banned acp cladding.
The ACP ban has created a number of risks that impacted
owners ought to consider:
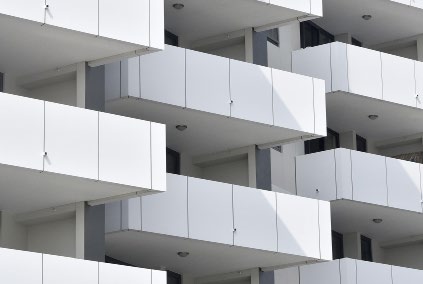
- Fire risk
- Council rectification orders
- Insurance changes – for your building, for your consultants
- A decrease in property value
- Difficulty selling property whilst
cladding affected - Capacity to obtain personal finance
(for a special levy) - Availability of qualified remedial contractors
Frequently asked questions
DO WE HAVE TO REMOVEÂ ALL OF THE BANNED ACP?
Legally, it depends. Pragmatically, full removal may best address your fire/life safety, legal, insurance and property value ‘risks’.
Is the government going to pay for this?
No. Not at this stage.
Will the council and Fire + Rescue NSW wait for us to resolve any legal claims before ordering us to remove the ACP cladding?
Probably not.
What if the ACP was deemed to comply with relevant building legislation at the time it was installed, surely we don’t have to remove it?
The ban operates retrospectively.
What about litigation, surely we can sue someone for this?
It is worth investigating but is unlikely to be fruitful for many owners. Likely to be costly and slow, with uncertain prospects
of success.
What are the risks in leaving some, or all, of the ACP cladding in situ?
Numerous ongoing ‘risks’ remain: fire/life safety, legal, insurance, and property saleability/value.
What’s happening?
• Building owners are under increasing pressure from Councils, insurers and/or concerned tenants to proceed
with the cladding remediation works.
• Many building owners will have to fund the cost of the remediation works themselves as the
parties responsible for the provision of the combustible cladding will likely deny liability, if they even still exist.
• Likewise many of these parties will no longer have any insurance to respond to any potential legal claims.
• The fire, legal, insurance and property value ‘risks’ are real – indecision and inaction isn’t the answer.
• Insurers have considerable power and have responded rapidly with premium increases.
• Professional indemnity insurance is evaporating by the day.
• ‘Partial replacements’ and ‘engineered solutions’ are unlikely to be approved.
• Litigation is likely to be very costly and slow, and is unlikely to be work for most owners.
• Council and Fire + Rescue NSW are increasingly risk-averse – post NEO200 fire.
• Property sales in cladding-affected buildings are being affected.
• Solid aluminum is the clear market preference for re-cladding
Combustible Cladding
Step-by-step remediation guide
Once all Stages are complete your fire risk will be reduced, your building can be removed from the NSWÂ Cladding Register, and your insurance premiums ought to normalise.
Step 1
Laboratory Testing
Laboratory testing of core hole samples of the existing cladding to determine if it is combustible and non-compliant. Testing to be undertaken by a qualified professional.
Step 2
Engage professionals to manage remediation process
Ensure that a suitable team of professionals are engaged to act on the client’s behalf and manage the cladding replacement process – including, client-side Project Manager, façade engineer, fire engineer, remedial building consultant and Private Certifier.
Step 3
Destructive investigation works
Undertake an investigation of the ‘build-up’ of the building’s external wall(s) (as defined by the BCA) to ensure there are no other combustible materials behind the cladding (eg, combustible insulation). This will require numerous panels of cladding to be temporarily removed and reinstated. The façade engineer should comment on the compliance and suitability of the existing cladding’s sub-framing and its connection methodology. These early-works aim to de-risk the project for all parties and reduce the number of ‘assumptions’ that are made about the make-up of the external wall(s).
Step 4
Preliminary quantities, budget and program
Based on the findings of the destructive investigation works, obtain preliminary – quantities (3D modeling), a budget price, and a program – to help inform your next decisions. How much is it likely to cost? how long is it likely to take? what is the extent of the likely inconvenience onsite?
Step 5
Finalise scope
Develop a final scope of works. Ensure this agreed scope of works is also acceptable to all key stakeholders – Private Certifier, Council, fire engineer, and insurer(s) – before commencing any works. Are there other general remedial works that should also be undertaken at the same time? Eg, waterproofing repairs, painting, concrete spalling etc.
Step 6
Remedial builder selection
Negotiate with a suitably experienced remedial builder or run a tender with various remedial builders. Choose wisely. For residential projects, your builder will need to obtain Home Warranty Insurance (HWI) to cover the remedial works (note, not all builders have HWI cover or are able to obtain it).
Step 7
Approval process for works
The works will likely need to be undertaken pursuant to a Development Application (DA), a Fire Safety Order or a Building Product Rectification Order. Note, coercive Orders will typically ask for the replacement material(s) to be ‘like for like’, to ensure the building’s facade looks the same at the end of the works. However, if you want to change the façade’s colour(s), or the ‘look and feel’ of the façade material(s) you will need to put in a DA, even if the works have been originated through a coercive Council Order.
Step 8
Finance
Many Strata’s will need to raise a Special Levy and/or obtain a Strata Loan (where the Strata itself borrows the funds). For residential projects, to enable the remedial builder to arrange Home Warranty Insurance the Strata will need to provide evidence to the Home Warranty Insurer of their capacity to pay for the works, prior to works commencing.
Step 9
Remediation works
Complete the works in accordance with the agreed scope. Ensure your team of professionals complete all required inspections, throughout the works.
Step 10
Project completion
Obtain all necessary project completion documents, including warranties and certificates, and store in a safe place. Provide all necessary completion documentation to all key stakeholders – Private Certifier, fire engineer, Council, and insurer(s).